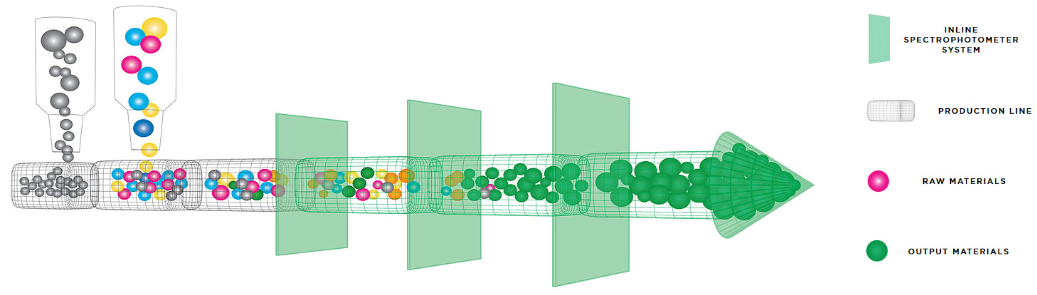
ColVisTec’s technology is designed to meet the needs of the plastics and polymers industry, offering robust, reliable, accurate spectroscopy even at high operating temperatures & pressures.
Understand and control your extrusion process → Improve product quality and efficiency.
We have more than 12 years’ combined experience in polymer extrusion & compounding with materials such as EVA, PP, PET, PVC, Nylon, and polycarbonates.
![]() |
![]() |
![]() |
||
![]() |